Download a pdf version of this data sheet for printing and future reference. (right click and select save to disk) |
431 Martensitic Stainless Steel Bar |
431 is a high chromium-low nickel high hardenability Martensitic stainless steel with high strength and good corrosion resistance, as generally supplied hardened and tempered in the tensile range 850 - 1000 Mpa (condition T) Brinell range 248 - 302.
Characterised by very good corrosion resistance in general atmospheric corrosive environments, good resistance to mild marine and industrial atmospheres, resistant to many organic materials, nitric acid and petroleum products coupled with high tensile and high yield strength plus excellent toughness in the hardened and tempered condition.
431 due to its excellent hardenability is capable of being through hardened up to Rc44, depending upon carbon content and section size. Small sections can be air cooled and larger sections oil quenched for maximum through hardness.
Pre hardened and tempered 431 will also respond readily to nitriding achieving a typical surface hardness of over Rc65. The nitriding process however reduces the corrosion resistance and is therefore not generally recommended except for critical applications where the benefit outweighs all other considerations.
Used extensively for parts requiring a combination of high tensile strength, good toughness and good corrosion resistant properties.
Typical applications are: Aircraft Parts and Components, Bolts and Nuts, Fasteners, Pump Shafts, Propellor Shafts, Studs, Valve Parts etc.
Material magnetic in all conditions.
|
Colour Code
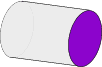 |
Purple
(Bar end) |
|
Stocked Sizes |
6.35 to 260 mm diameter. |
Bar Finish |
Peeled, Cold Drawn
Turned and Polished, and
Centreless Ground. |
Related Specifications |
|
Australia |
AS 2837-1986 431 |
Germany |
W.Nr 1.4057 X20CrNi17 2 |
Great Britain |
BS970 Part3 1991 431S29
BS970 - 1955 EN57 |
Japan |
JIS G4303 SuS 431 |
USA |
ASTM A276-98b 431
SAE 51431 AISI 431
UNS S43100 |
Chemical Composition |
Min. % |
Max. % |
|
Carbon |
0.12 |
0.20 |
Silicon |
0 |
1.00 |
Manganese |
0 |
1.00 |
Nickel |
1.25 |
3.00 |
Chromium |
15.00 |
18.00 |
Phosphorous |
0 |
0.04 |
Sulphur |
0 |
0.03 |
Mechanical Property Requirements For Material in the Annealed and Heat Treated - Condition T To AS2837 - 1986 431 and BS970 Part3 1991 431S29 |
|
Condition |
Tensile
Strength
Mpa
Min Max |
0.2% Yield
Strength
Mpa
Min |
Elongation
on 5.65
%
Min |
Izod Impact Value
Section
Size J
mm Min |
Hardness
HB |
|
Min |
Max |
Annealed |
|
|
|
|
|
277 |
*T |
850 1000 |
635 |
11 |
63 34
63 20 |
248 |
302 |
*Material stocked generally in condition T.
NB. Check the mill certificate if critical for end use. |
Typical Mechanical Properties At Room Temperature - *Hardened and Tempered to Condition T |
|
Tensile
Strength
Mpa |
Yield
Strength
Mpa |
Elongation
in 50mm
% |
Impact
Izod
J |
Hardness |
|
HB |
Rc |
940 |
750 |
19 |
65 |
280 |
30 |
*Typical Hardening Temperatures |
|
980 oC - 1020 oC |
*Typical Double Tempering Temperatures |
1) |
640 oC - 660 oC |
|
2) |
590 oC - 610 oC |
|
Typical Mechanical Properties At Room Temperature - Hardened By Oil Quench at 980 oC and Tempered as Indicated |
|
Tempering
Temperature
oC |
Tensile
Strength
Mpa |
Yield
Strength
Mpa |
Elongation
in 50mm
% |
Impact
Charpy
J |
Hardness |
|
HB |
RC |
250 |
1370 |
1030 |
16 |
54 |
410 |
44 |
370 |
1390 |
1130 |
16 |
*34 |
420 |
45 |
480 |
1410 |
1200 |
16 |
*16 |
425 |
46 |
590 |
980 |
790 |
19 |
65 |
295 |
32 |
650 |
920 |
690 |
20 |
70 |
270 |
29 |
High tensile strength and high yield strength with slightly lower impact properties when tempered below 370 oC.
Section Size 30mm
*Note drop in impact properties. Tempering within the range 370 oC - 565 oC should be avoided.
|
Elevated Temperature Properties |
431 displays good resistance to scaling in continuous service up to 700 oC. Its use however at these higher working temperatures results in a substantial drop in tensile strength and hardness, with subsequent increase in ductility.
|
Typical Mechanical Properties at Elevated Temperatures, Hardened at 1010 oC and Tempered at 30 oC Above Working Temperature |
|
Tempering
Temperature
oC |
Working
Temperature
oC |
Tensile
Strength
Mpa |
Elongation
in 50mm
% |
Room Temperature
Hardness after Test |
|
HB |
Rc |
510 |
480 |
1350 |
15 |
440 |
47 |
570 |
540 |
720 |
20 |
330 |
37 |
620 |
590 |
435 |
26 |
280 |
30 |
NB. Creep and stress rupture strength is also substantially reduced at these higher working temperatures.
|
Low Temperature Properties |
431 is not recommended for use at sub-zero temperatures due to a substantial drop in impact properties consistent with most steels other than the austenitic steel types.
|
Cold Bending |
In the hardened and tempered as supplied condition will be extremely difficult due to the high yield strength and is not generally recommended.
|
Hot Bending |
In the hardened and tempered as supplied condition it is not recommended due to its affect on the mechanical properties within the heat affected zone.
|
Corrosion Resistance |
431 has the highest corrosion resistance of all the Martensitic stainless steels, and while not as high as the austenitic stainless steels it is in certain corrosive environments similar to that of 301 and 302 grades.
NB. It has optimum corrosion resistance in all environments in the hardened and tempered condition, and is not therefore recommended for use in the annealed condition.
It is most important that oxygen is always allowed to circulate freely on all stainless steel surfaces to ensure that a chrome oxide film is always present to protect it. If this is not the case, rusting will occur as with other types of non stainless steels.
For optimum corrosion resistance surfaces must be free of scale and foreign particles.
Finished parts should be passivated.
|
Forging |
Heat uniformly to 1150 oC - 1200 oC, hold until temperature is uniform throughout the section. Do not soak but commence forging immediately.
Do not overheat as this will cause a loss of toughness and ductility.
Do not forge below 900 oC
Finished forgings should be cooled as slowly as possible in dry lime or ashes to room temperature and sub-critical annealed immediately.
|
Heat Treatment |
Sub-Critical Annealing |
Heat uniformerly to 620 oC - 660 oC hold until temperature is uniform throughout the section.
*Soak as required - suggested time 6 to 12 hours but can be longer, cool in air.
|
Hardening |
Heat to 950 oC - 1020 oC, hold until temperature is uniform throughout the section. *Soak as required.
Quench in oil or air cool. Temper immediately while still hand warm.
Note: Best impact properties achieved by hardening from above 1020 oC. Best corrosion resistance plus mechanical properties achieved by hardening from about 980 oC and tempering above 590 oC.
|
Nitriding |
Prior to nitriding, the chrome oxide film which protects the surface must be broken down by pickling or fine sand blasting.
Nitriding is carried out at 500 oC - 550 oC followed by slow cooling (no quench) reducing the problem of distortion. Parts can therefore be machined to near final size, leaving a grinding tolerance only. Always ensure that the tempering temperature employed during the initial heat treatment was higher than the nitriding temperature otherwise the core strength will be affected.
|
Tempering (Condition T) |
Heat to 590 oC - 680 oC as required hold until temperature is uniform throughout the section, soak as required, cool in air.
|
A Double Tempering Treatment, as follows is recommended for optimum toughness. |
Heat to 640 oC - 680 oC. *Soak as required, cool in air.
Followed by:
Re heat to 590 oC - 610 oC. *Soak as required, cool in air.
431 can of course be tempered at much lower temperatures producing much higher tensile strengths with subsequent lower impact properties.
NB. Tempering however within the range 370 oC - 565 oC should be avoided due to temper brittleness, resulting in a considerable reduction in impact properties and loss of corrosion resistance.
*Heating temperatures, rate of heating, cooling and soaking times will vary due to factors such as work piece size/shape, also furnace type employed, quenching medium and work piece transfer facilities etc.
Please consult your heat treater for best results.
|
Machining |
431 machines best in the hardened and tempered as supplied condition and is regarded as being readily machineable with all operations such as turning and drilling etc. capable of being carried out satisfactorily. It does not work harden to the same extent as the 300 series austenitic stainless steels, but is more similar in this respect to the low alloy high tensile steels such as 4140 etc.
Allowing therefore for its high tensile properties, all machining should be carried out as per machine manufacturers recommendations for suitable tool type, feeds and speeds.
|
Welding |
431 is not generally recommended for welding in either the annealed or hardened and tempered condition, due to its air hardening capability which can lead to the formation of brittle martensite, resulting in cold cracking due to contraction stresses within the weld and heat affected zone. The higher the carbon content the higher the hardening capability and the greater the risk of cracking.
Pre heating and interpass temperature control during welding, plus very slow cooling and post-weld annealing is the best method to prevent cracking.
The following welding procedure and post-weld heat treatment may be taken as a guide only if welding is necessary.
|
Welding Procedure |
Welding electrodes or rods should be low hydrogen types 410 or *similar when good strength is required otherwise an austenitic stainless electrode or rod such as 308 or *similar may be used resulting in a more ductile weld when strength is not so critical and post-weld annealing is not possible or intended.
Pre-heat at 200 oC - 300 oC and maintain interpass temperature at 200 oC minimum. On completion of welding cool slowly as possible until hand warm if possible:
Post-weld sub-critical anneal at 620 oC - 660 oC, and cool in air.
*Please consult your welding consumables supplier.
|
Interlloy believes the information provided is accurate and reliable. However no warranty of accuracy, completeness or reliability is given, nor will any responsibility be taken for errors or omissions. |
|